Flange Facer Machine: Essential Tool for Precision Flange Resurfacing
May 16, 2025 | News | No Comments
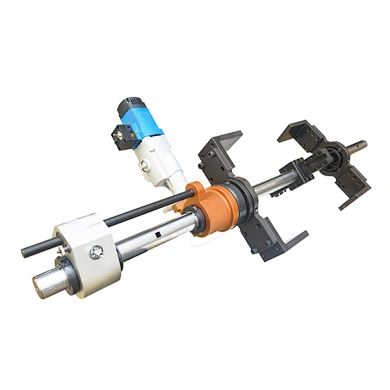
# Flange Facer Machine: Essential Tool for Precision Flange Resurfacing
## What is a Flange Facer Machine?
A flange facer machine is a specialized industrial tool designed for resurfacing and machining flange faces to ensure proper sealing and alignment in piping systems. These powerful machines play a critical role in maintaining pipeline integrity by creating perfectly flat and smooth sealing surfaces on flanges.
## Key Features of Modern Flange Facers
Modern flange facer machines incorporate several important features:
– Portable design for on-site machining
– Precision cutting tools for accurate resurfacing
– Adjustable mounting systems for various flange sizes
– Automated feed mechanisms for consistent results
– Dust collection systems for cleaner operation
## Applications in Various Industries
Flange facer machines serve essential functions across multiple sectors:
### Oil and Gas Industry
In pipeline systems, these machines ensure proper sealing of high-pressure connections, preventing dangerous leaks in critical infrastructure.
### Power Generation Plants
They maintain the integrity of steam and coolant systems by providing perfectly machined flange surfaces in turbines and heat exchangers.
### Chemical Processing Facilities
Precision-faced flanges prevent hazardous material leaks in corrosive environments where sealing integrity is paramount.
### Water Treatment Plants
These machines help maintain large diameter piping systems that transport water and treatment chemicals.
## Benefits of Using Flange Facer Machines
Implementing flange facer technology offers numerous advantages:
– Eliminates the need for complete flange replacement
– Reduces downtime during maintenance
– Ensures perfect sealing surfaces
– Lowers maintenance costs significantly
– Improves safety by preventing leaks
– Extends the service life of existing flanges
## Choosing the Right Flange Facer Machine
When selecting a flange facer, consider these factors:
– Maximum and minimum flange diameter capacity
– Power source requirements (electric, hydraulic, or pneumatic)
– Portability and weight
– Cutting tool options and specifications
– Automation features
– Available accessories and attachments
## Maintenance Tips for Optimal Performance
To ensure long-term reliability of your flange facer machine:
– Regularly inspect and replace cutting tools
– Keep all moving parts properly lubricated
– Clean the machine after each use
Keyword: flange facer machines
– Store in a dry, protected environment
– Follow manufacturer’s maintenance schedule
– Train operators in proper usage techniques
## The Future of Flange Facing Technology
Advancements in flange facer machines include:
– Improved automation with digital controls
– Enhanced portability features
– Smart monitoring systems
– More efficient cutting tool materials
– Integration with measurement systems
– Environmentally friendly designs
Flange facer machines represent an essential investment for any operation relying on piping systems. By maintaining perfect sealing surfaces, these tools prevent costly leaks, reduce downtime, and extend the life of critical infrastructure components.