Die Casting Process Optimization Techniques
July 17, 2025 | News | No Comments
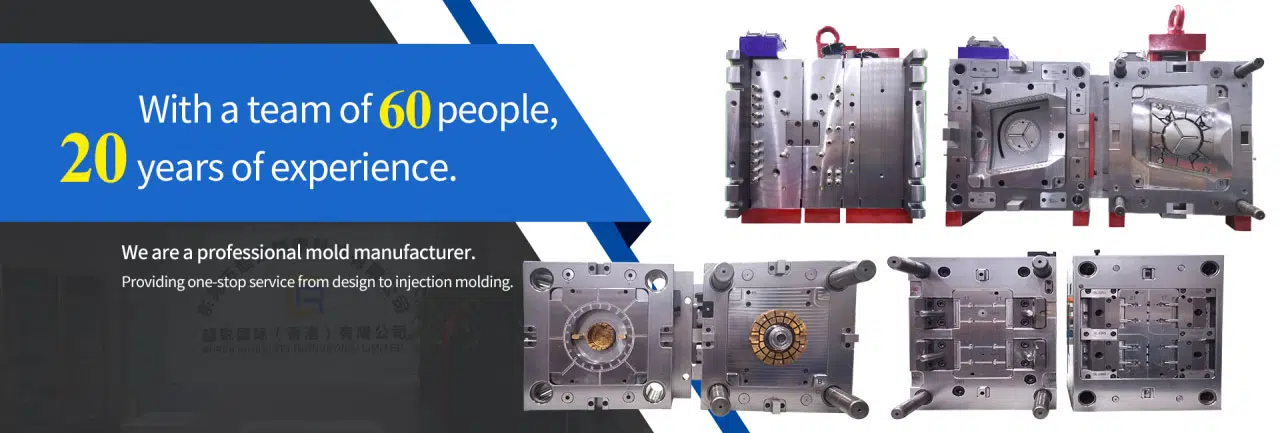
# Die Casting Process Optimization Techniques
## Introduction to Die Casting Optimization
Die casting is a highly efficient manufacturing process that produces precise metal parts with excellent surface finishes. However, to maximize productivity and quality while minimizing costs, manufacturers must continually optimize their die casting processes. This article explores key techniques for improving die casting operations.
## Key Optimization Areas
### 1. Mold Design Improvements
Optimizing mold design is crucial for successful die casting. Consider these approaches:
- Implement conformal cooling channels to improve heat transfer
- Use simulation software to predict and prevent potential defects
- Optimize gate and runner systems for better metal flow
- Select appropriate mold materials for longevity
### 2. Process Parameter Optimization
Careful control of process parameters significantly impacts casting quality:
- Precise temperature control of molten metal and dies
- Optimal injection speed and pressure profiles
- Proper lubrication application timing and quantity
- Accurate cycle time determination
## Advanced Optimization Techniques
### 3. Real-Time Monitoring Systems
Implementing advanced monitoring systems allows for:
- Continuous tracking of critical process variables
- Early detection of process deviations
- Data collection for predictive maintenance
- Automated quality control checks
### 4. Material and Energy Efficiency
Optimizing material and energy usage reduces costs and environmental impact:
- Implement scrap recycling programs
- Use energy-efficient melting and holding furnaces
- Optimize shot weight to minimize material waste
- Recover and reuse thermal energy
Keyword: Die Casting
## Implementation Strategies
Successful optimization requires a systematic approach:
- Conduct thorough process audits to identify improvement opportunities
- Prioritize changes based on potential impact and implementation difficulty
- Test changes on a small scale before full implementation
- Train operators on new procedures and technologies
- Establish metrics to measure improvement effectiveness
## Conclusion
Die casting process optimization is an ongoing journey that requires attention to detail, technological adoption, and continuous improvement. By implementing these techniques, manufacturers can achieve higher quality products, increased productivity, and reduced operational costs, ensuring competitiveness in today’s demanding manufacturing environment.