Sanitary Pad Pouch Manufacturer
June 19, 2025 | News | No Comments
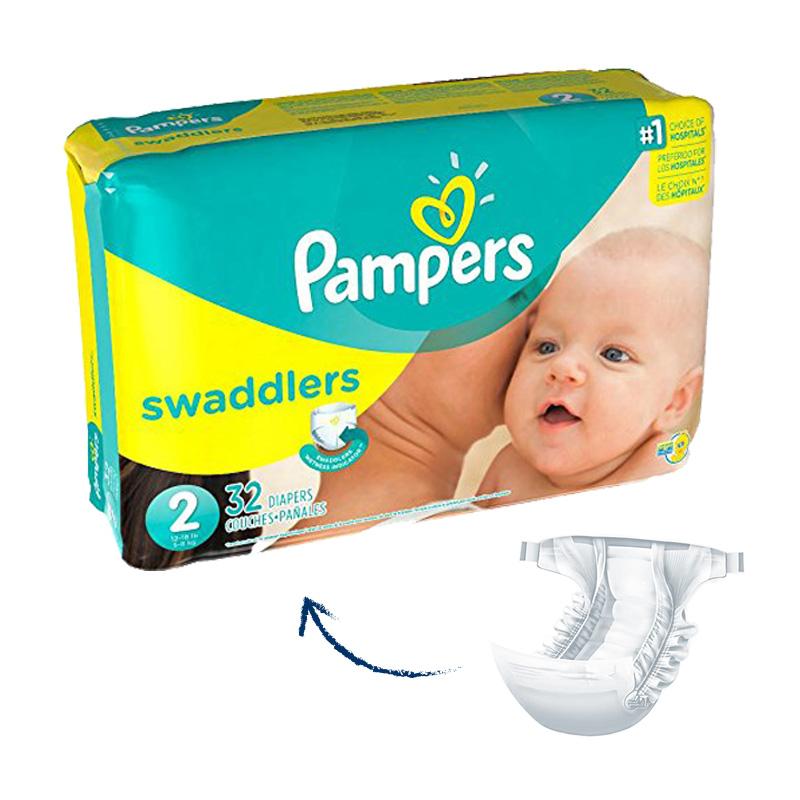
# Sanitary Pad Pouch Manufacturer: Quality and Discretion in Feminine Hygiene
## The Importance of Sanitary Pad Pouches
In today’s fast-paced world, women need discreet and convenient solutions for carrying sanitary pads. A reliable sanitary pad pouch manufacturer understands this need and creates products that combine functionality with style. These pouches serve multiple purposes – they protect feminine hygiene products from damage, maintain cleanliness, and provide privacy when carrying pads in public spaces.
## What Makes a Quality Sanitary Pad Pouch?
When choosing a sanitary pad pouch manufacturer, several factors determine product quality:
Keyword: sanitary pad pouch manufacturer
– Durable materials that withstand daily use
– Water-resistant or waterproof fabrics
– Discreet designs that don’t draw attention
– Adequate size to hold multiple pads
– Easy-to-clean surfaces
– Secure closures (zippers, snaps, or Velcro)
## Manufacturing Process of Sanitary Pad Pouches
Professional sanitary pad pouch manufacturers follow strict production processes to ensure consistency and quality:
1. Material selection – Choosing fabrics that are soft, durable, and easy to clean
2. Pattern design – Creating templates for various pouch sizes and styles
3. Cutting – Precision cutting of fabric pieces
4. Sewing – Assembling components with reinforced stitching
5. Quality control – Inspecting each pouch for defects
6. Packaging – Preparing products for shipment
## Customization Options from Manufacturers
Many sanitary pad pouch manufacturers offer customization services to meet specific client needs:
– Branded pouches with company logos
– Various color options to match brand identities
– Different size configurations
– Special fabric choices (organic cotton, recycled materials)
– Additional features like inner pockets or key rings
## Environmental Considerations in Production
Leading sanitary pad pouch manufacturers are increasingly focusing on sustainable practices:
– Using eco-friendly materials
– Implementing waste reduction programs
– Offering reusable pouch options
– Developing biodegradable packaging
– Reducing water and energy consumption in production
## Choosing the Right Manufacturer
When selecting a sanitary pad pouch manufacturer for your business needs, consider:
– Production capacity and lead times
– Minimum order quantities
– Quality control measures
– Compliance with international standards
– Experience in the feminine hygiene market
– Customer service and communication
## The Future of Sanitary Pad Pouches
As awareness about feminine hygiene grows globally, sanitary pad pouch manufacturers are innovating with:
– Smart pouches with tracking features
– Antimicrobial fabrics
– Temperature-controlled designs
– Multi-functional pouches that also hold other personal items
– Fashion-forward designs that make pouches style statements
By partnering with a reputable sanitary pad pouch manufacturer, businesses can offer women practical, stylish solutions that address an essential need while maintaining discretion and convenience in their daily lives.