Sanitary Pad Packaging Bag: Essential Features and Benefits
June 15, 2025 | News | No Comments
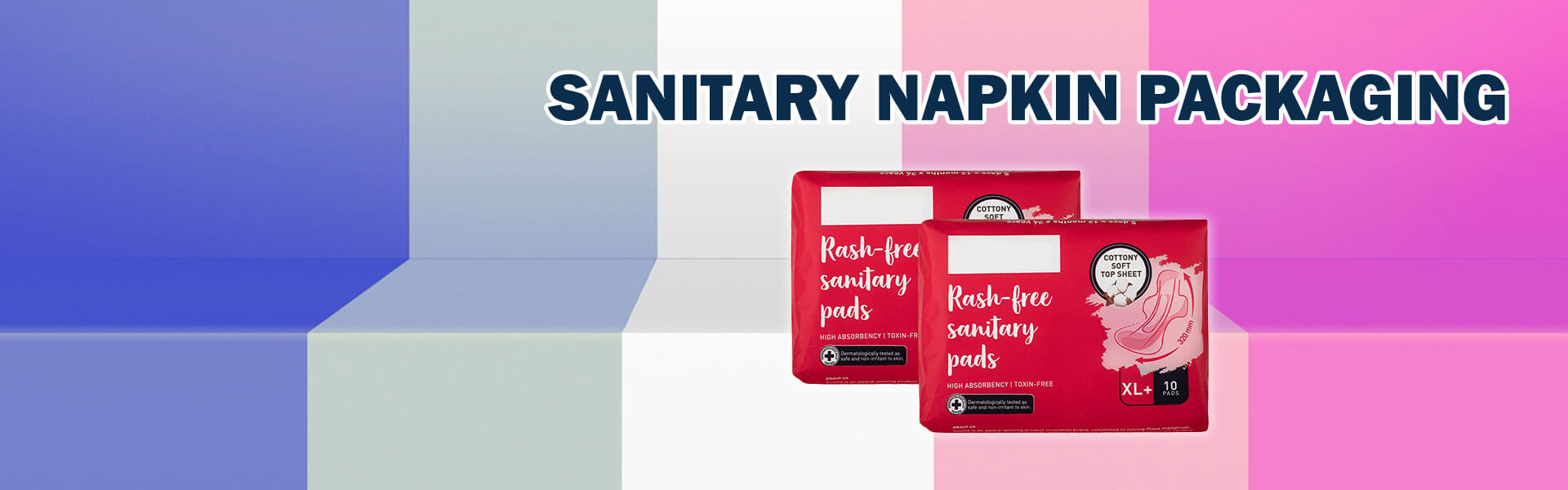
# Sanitary Pad Packaging Bag: Essential Features and Benefits
## Introduction to Sanitary Pad Packaging Bags
Keyword: sanitary pad packaging bag
Sanitary pad packaging bags play a crucial role in maintaining hygiene and convenience for women during their menstrual cycles. These specialized bags are designed to store and carry sanitary pads discreetly while protecting them from contamination.
## Key Features of Quality Sanitary Pad Packaging Bags
### 1. Moisture-Resistant Material
High-quality packaging bags are made from moisture-resistant materials that prevent dampness from affecting the pads inside. This ensures the sanitary products remain dry and ready for use.
### 2. Odor-Controlling Properties
Many premium packaging bags incorporate odor-control technology to maintain freshness and discretion, especially important when carrying used pads before proper disposal.
### 3. Compact and Portable Design
Modern sanitary pad bags feature slim, lightweight designs that easily fit into purses, backpacks, or even pockets for ultimate convenience.
### 4. Discreet Appearance
Discretion is a priority, with many bags designed to look like ordinary cosmetic cases or small pouches rather than obvious menstrual product carriers.
## Benefits of Using Specialized Sanitary Pad Packaging Bags
### Enhanced Hygiene Protection
By keeping pads in dedicated packaging, users prevent contamination from other items in their bags and maintain better personal hygiene standards.
### Improved Organization
These bags help women stay organized by providing a designated space for both fresh and used pads, along with disposal bags when needed.
### Travel-Friendly Solution
Sanitary pad packaging bags make it easier to carry menstrual products while traveling, ensuring women have what they need when away from home.
### Environmental Considerations
Many eco-conscious brands now offer reusable packaging bags made from sustainable materials, reducing waste from disposable plastic wrappers.
## Choosing the Right Sanitary Pad Packaging Bag
When selecting a packaging bag, consider:
– Size requirements based on your preferred pad type
– Material durability and ease of cleaning
– Additional features like separate compartments
– Style preferences that match your personal taste
– Environmental impact of the materials used
## Maintenance and Care Tips
To ensure longevity of your sanitary pad packaging bag:
– Regularly clean the interior with mild soap and water
– Allow to air dry completely before reuse
– Avoid overfilling to maintain the bag’s shape
– Replace when signs of wear or odor retention appear
## Conclusion
Investing in a quality sanitary pad packaging bag offers numerous benefits for women seeking convenience, discretion, and improved hygiene during their menstrual cycles. With various options available on the market, finding one that meets individual needs and preferences has never been easier.